Regarding your idea
In what consist your idea ?
The overall idea is to fill the gap between a turning machine and an ultraprecision turning machine. Décolletage is a machining technology that can provide finished complex parts from a bar in high pace with, in optimal conditions, process reliability for big batches with tolerances down to 10 micrometres. Ultraprecision manufacturing is a technology that can provide extreme precision and high-quality surfaces with tolerances below one micrometre. The higher precision in ultraprecision application, e.g. for optical surfaces, can be reached by given processes like diamond turning thanks to a very precise machine, but typically in non-ferrous metals with strongly reduced degrees of freedom on the machine. The aim of the project is to understand if and which compromises can be reached between these two technologies and what the potential in the current market is.
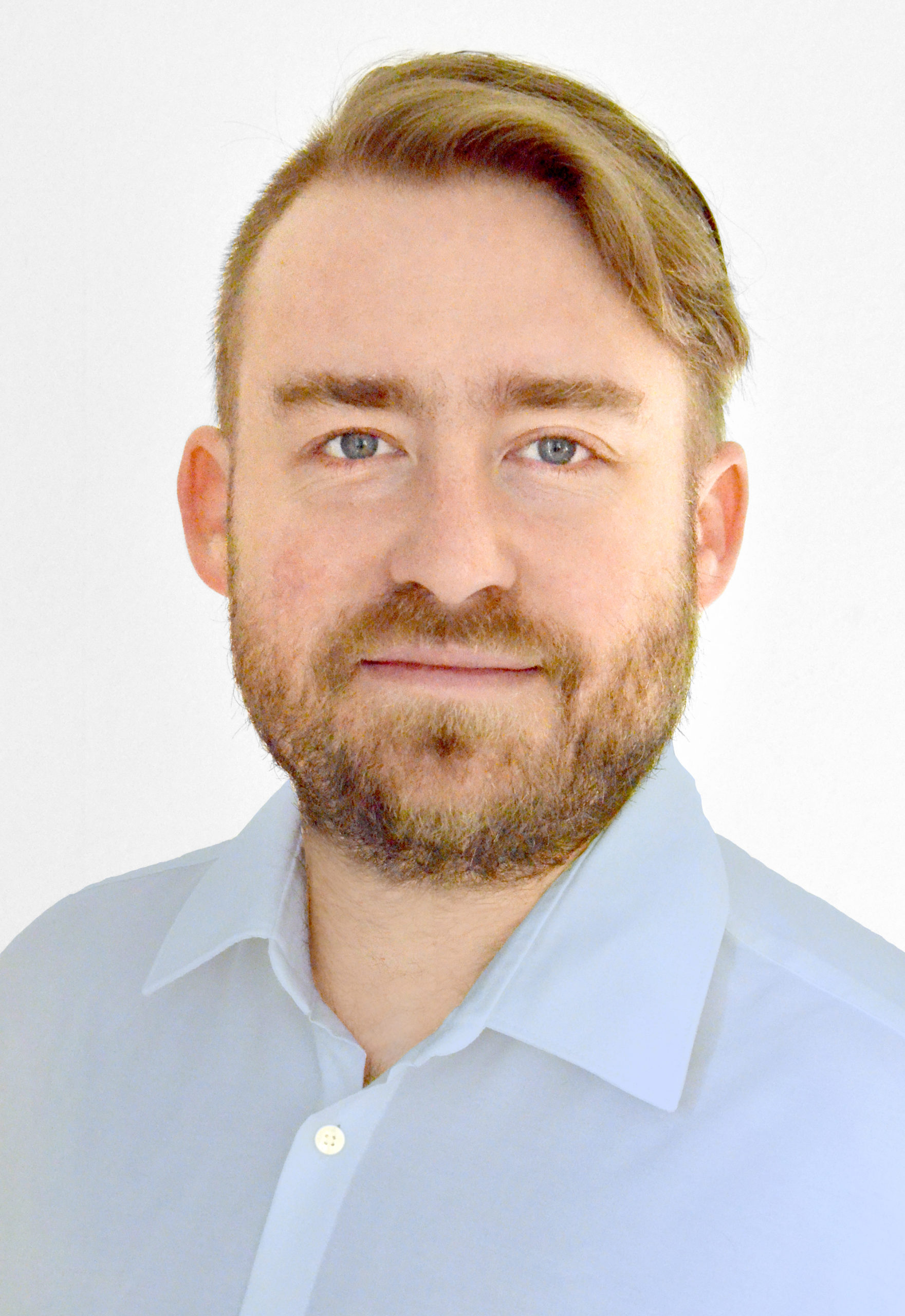
Raoul Roth, Project Manager at RhySearch in Buchs (SG).
Who is this innovation for?
As applied research centres, RhySearch and inspire are confronted with the limits of today’s industry. Companies notice the limits especially when the “market pull” asks for new generation of products, which are not feasible with current technologies. With the well-known trends of miniaturization as well as digitalisation and demand of higher data transfer rates, smaller components with tighter tolerances and better surface quality are needed. In this sense the innovation addresses manufacturers with Décolletage machines, which cannot satisfy the requested precision and process reliability with sufficient profitability.
Precision is depending on various factors, the machine tool, the tooling, the process parameters, the material, the lubricant system, and many others. Therefore, with the proposal, we try to addresses every player in the ecosystem of enabling technologies, so that a roadmap for the next generation can be drawn.
Who will be the end user of this innovation?
The primary beneficiaries of the feasibility study are the technology enablers around Décolletage. Thanks to the feasibility study the main technologies which have to be addressed to satisfy the future needs of the market can be better identified. In a second step, the manufacturing companies struggling with the limits of feasibility and process stability of the produced components can profit, having the possibility to enhance their production.
In which application areas could this innovation be useful?
As mentioned before, the resulting innovation, which may be developed in one or more following projects, will enhance the precision of a highly automatized production of tiny turning parts. This means an enhancement of the process precision and reliability of Décolletage machines.
Why do you want to develop this idea?
The motivation arises from companies which typically are successfully producing high precision parts with high process reliability with a high degree of automation, but cannot satisfy the newest trend of the designs with the same profitability. This means that the new design can be produced only with a significantly higher effort and correspondent cost or may not even be produced with current technologies. With the support of the innovation booster we would like to address this topic and check, in the feasibility study, the technical and economic potential of possible new technologies and strategies. The result is a first guide, or roadmap how we call it, for the next generation of Décolletage machines.
What benefits will this bring to users?
The manufacturing industry, so the costumer of the technology enablers, has an advantage by showing directly their needs in an early development stage. Therefore, beside quick wins, that may arise during following projects, they have the possibility to shape the future markets fitting to their needs.
Regarding the Microtech Booster
You are one of the winners of the Microtech Booster. Who are your partners in this project?
The idea we proposed has been joint by two type of partners. First two companies which define the present and future demand of high precision machining. Kistler uses Décolletage machines especially for their production of force and acceleration sensors, technology in which the company is worldwide leader. Jabil, which production in Switzerland is focused on medical, also uses Décolletage machines for examples for the production of implants. Secondly Tornos, a Swiss producer of Décolletage machines complements the team with the know how and the interests of the provider of the crucial enabling technology. Last but not least two research centres, RhySearch and inspire, which commonly proposed the idea. inspire has a long track of research experience in a broad variety of machining processes, while RhySearch is a younger institute with a strong focus on high and ultra-precision technology.
What are your objectives for the realization of the feasibility study of your project, supported by the 20 KCHF from InnoSuisse?
The long-term overall goal is the development and realization of one optimized décolletage machine with high process reliability. We quantified some goals as for example, the enhancement of workpiece precision with high process reliability below 0.002 mm, to agree on a general direction.
But now we have to focus on the goals of the Microtech Booster program, and this feasibility study. Here we aim to understand the feasibility of combining ultra-precision technologies in more flexible and efficient systems (i.e. décolletage machine). To reach this, we first have to analyse the sources and causes of different inaccuracies happening during processes affecting the precision of the end-parts and evaluate potential of applying technologies as they are known for example in today’s ultra precision machine tools.
What do you expect from the Microtech Booster platform during the next 6 months?
The platform helped us already before the start of the study giving us visibility on their network and beyond. This was really important for us to, on one hand, see if the idea gets the supposed interest and on the other side gathering together the crucial player. Furthermore, the platform gives us interesting inputs how to organize and implement the project from a legal point of view as well as tools to exchange data in the team.
More about you
What is your professional background?
After my studies in mechanical engineering at ETH Zürich, I started my research career in the topic of machining processes working for inspire AG. Always in tight collaboration with swiss industry, I had the opportunity to accomplish my Doctoral studies at the Institute for Machine Tool and Manufacturing (IWF) of ETH Zürich, exploring new technologies in the world electrical discharge machining. After a short experience at the Institute of Sustainable Development of ZHAW, I returned to IWF of ETH Zürich for a Postdoc in the topic of surface functionalization by means of electrical discharge machining and laser technologies.
Where are you currently working?
After my Postdoc at ETH, I joined RhySearch in 2017. As first collaborator of the newly coined group for applied research in precision machining, I had the great opportunity to shape the fast-developing group.
What position do you hold there?
I still enjoy my work as a project manager for research projects in tight collaboration with the Swiss industry.