About your idea
In what consist your idea ?
In the inspire Materials, Processes and Sustainability group, together with Advanced Manufacturing Laboratory of ETH Zürich and the start-up Sallea, a novel 3D shaping technology is being developed.
“Shaping the unshapable”: this mission brings together two innovative processes, to produce parts with unprecedented material properties, freeform and hollow shapes.
We combine
- an ultra-fast Spark Plasma Sintering (SPS) process,
- with additively manufactured water-soluble lost molds,
- to produce 3D metal parts.
Additive manufacturing with unconventional materials – be part of the challenge!
Who will be the final user of your idea ?
Are you interested in metallic materials and compounds that can hardly be additively manufactured?
Do you need subtractive manufacturing to shape components with your material?
Or do you want to apply near net shaping with 100% material usage?
The users of our technology will be able to near-net-shape difficult and expensive materials. Brought to us by watchmakers as ultimate challenge, we focus now on bulk metallic glasses (BMGs). Other materials are tested and can be applied more easily: pure copper, metal matrix composites (WC-Co), precious metals (Gold), to name a few.
In which fields this idea would be useful ?
From watchmaking to medtech, from tooling to fluidics. The field of application is vast. It’s all about small, complex geometries, made from materials that are unconventional, hard, brittle, expensive, etc.
What will the benefits of your idea ?
Focusing on BMGs now: This material group is extremely hard to manufacture. Only a handful can be additively manufactured, even then with tremendous restrictions due to their brittleness.
By exploring our new method to near net shape complex structures, many BMG alloys can finally be free-formed with hollow structures, internal channels etc. This is realized by fast sintering instead of melting, which retains the amorphous (glass-like) internal structure.
Due to their exceptional properties, like resistance to scratching and corrosion, and high hardness and elasticity, BMGs are applied in watchmaking, jewelry, medtech, and other innovative fields.
What kind of partner are you looking for to invest in your idea and be part of your team ?
The wish to bring shape to BMGs came from the watchmaking sector. But it doesn’t stop there. We’re looking for partners in all fields that could benefit: jewelry, medtech, fluidics, tooling, etc.
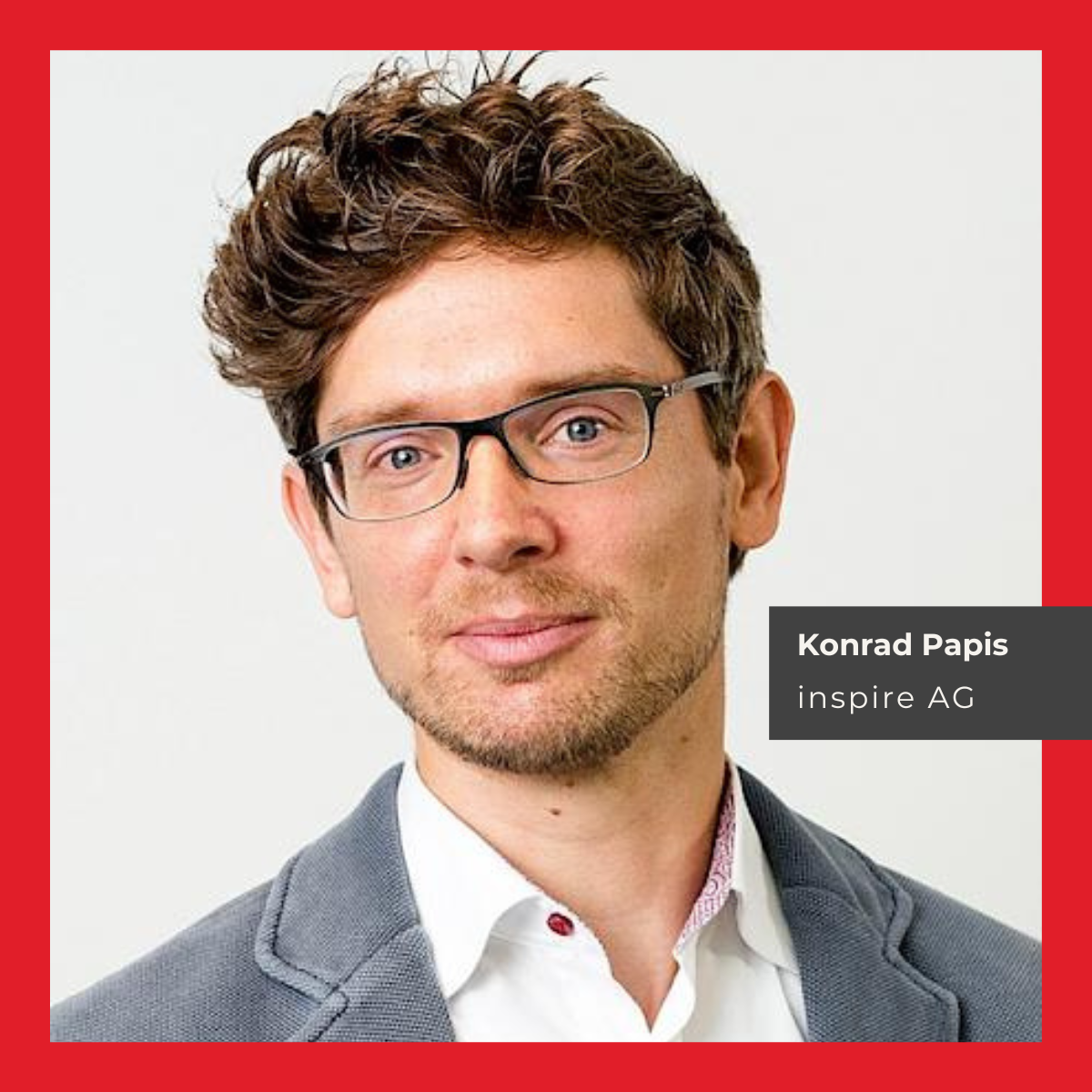
How have you heard about the Microtech Booster ?
I was asked to place this idea on the MT Booster from a consortium in the Swiss watchmaking industry.
What are your exceptings about the Microtech Booster ?
I expect visibility of the idea to relevant industry partners, and a lively discussion about their questions, hopes, doubts and applications.
About you and the Booster
Who are you ?
My name is Konrad Papis, I was born in Vienna/Austria. I’m a materials engineer with 10 years’ experience in the Swiss manufacturing industry.
I graduated from ETH as PhD, and worked in small and large Swiss companies, always in collaboration with academia and production.
Three years ago, I switched sides of the table, now picking up challenges from industry: in a collaboration with industry and academia, I work on sustainable solutions for materials in advanced manufacturing.
In which company are you working now and what’s your occupation/position ?
Inspire AG is a strategic partner to ETH for technology transfer in advanced manufacturing. I’m leading the group of “Materials, Processes and Sustainability”.
Would you like to participate in this idea?
Join the team on the platform.